Iron and Steel
Mechanical Seals for Iron and Steel Industry
Iron and Steel
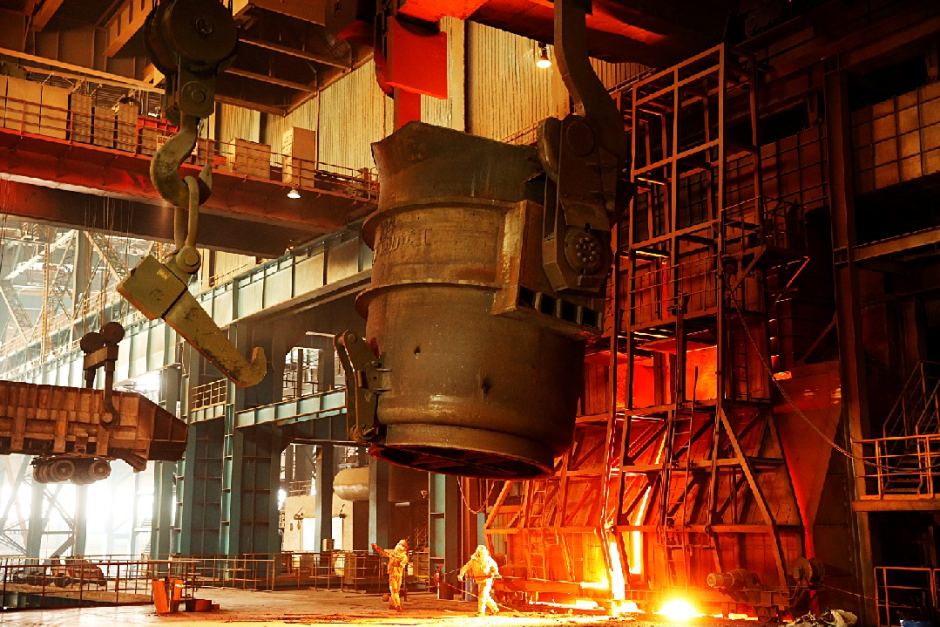
Mechanical seals for iron and steel sector
Mechanical seals used in the iron and steel sector need to withstand high temperatures, abrasive materials, and often corrosive environments
Mechanical seals used in the iron and steel sector need to withstand high temperatures, abrasive materials, and often corrosive environments. Here are some considerations for mechanical seals designed for this sector:
- High-Temperature Resistance: Seals must be able to withstand the high temperatures found in steel manufacturing processes, such as those encountered in blast furnaces, steel casting, and rolling mills.
- Abrasion Resistance: Given the abrasive nature of many materials used in the iron and steel industry, mechanical seals should be constructed from materials capable of withstanding wear, such as silicon carbide, tungsten carbide, and ceramics.
- Corrosion Resistance: Seals must resist corrosion from acids, alkalis, and other chemicals present in steel manufacturing processes. Stainless steel, Hastelloy, and other corrosion-resistant materials are commonly used.
- Robust Mechanical Seal Design: The seals should have a robust design capable of withstanding the harsh operating conditions commonly found in the iron and steel industry, including heavy loads and vibration.
- Mechanical Seal Face Configuration: The seal face configuration should be designed to minimize wear and prevent leakage, even in high-pressure environments.
- Flush Plans: Flush plans may be necessary to prevent the buildup of contaminants around the seal faces. This involves using a clean fluid to flush the seal area, ensuring proper lubrication and cooling.
- Mechanical seal Cooling Systems: Cooling systems may be required to prevent overheating of the seal faces, especially in high-temperature applications. This helps to extend the life of the seals and improve reliability.
- Pressure and Temperature Ratings: Seals must be rated for the specific pressure and temperature conditions present in iron and steel manufacturing equipment.
- Ease of Maintenance: Maintenance of mechanical seals in the iron and steel sector can be challenging due to the harsh operating conditions. Seals should be designed for easy installation, inspection, and replacement.
- Supplier Support and Service: Working with a supplier who has experience in providing mechanical seals for the iron and steel industry is important. They should offer technical support and service to ensure optimal performance and reliability.
By considering these factors, mechanical seals can be designed and selected to effectively seal equipment in the iron and steel sector, ensuring reliable operation and minimizing downtime.
Sealomech Engineering one of the leading seal manufacturers in India providing standard & customized sealing solutions to clients across industries, with its wide range of seal profiles and elastomers is fully capable of serving Iron & Steel Industries.
Email Us: info@sealomech.com or Call Us: +91-8898230000